So the run of Nacelle Clips is underway in Hong Kong right now but a friend who works for a company with a new type of 3D printer that produces parts that are much smoother than other types of printers offered to print a couple test parts for me. I thought that rather than just try to print some end use parts that it would be cool to try to print "embedded" two part mold patterns. And the Nacelle Clips was the perfect part to test. Traditionally the original pattern part (either scratch build or 3D printed, would be embedded in clay up to the half way point and one side of the mold poured. Then after the rubber was cured, the clay would be cleaned off and rubber poured on the other side creating a two part mold. It can be very time consuming to clay up the part, especially small or highly detailed and irregular parts like the clip. In addition, If I wanted to be able to cast a lot of parts I'd need a gang mold, which would mean claying up a bunch of parts. Way too much work!
Instead, since the part was 3D modeled, I basically made two separate 3D models of a set of four of the parts, side by side, as they would be embedded in a mold surface, complete with keys and a fill port. There were two models, one for each side. These were then 3D printed at high resolution.
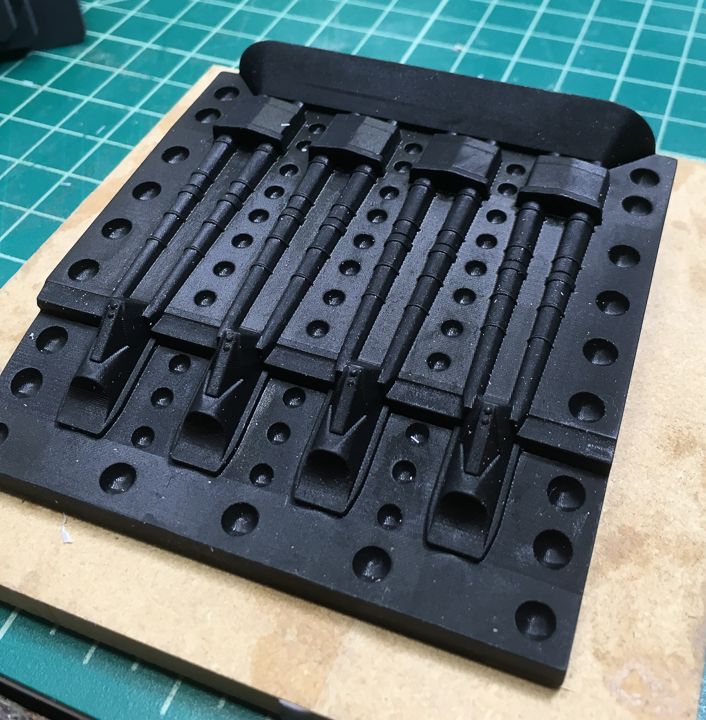
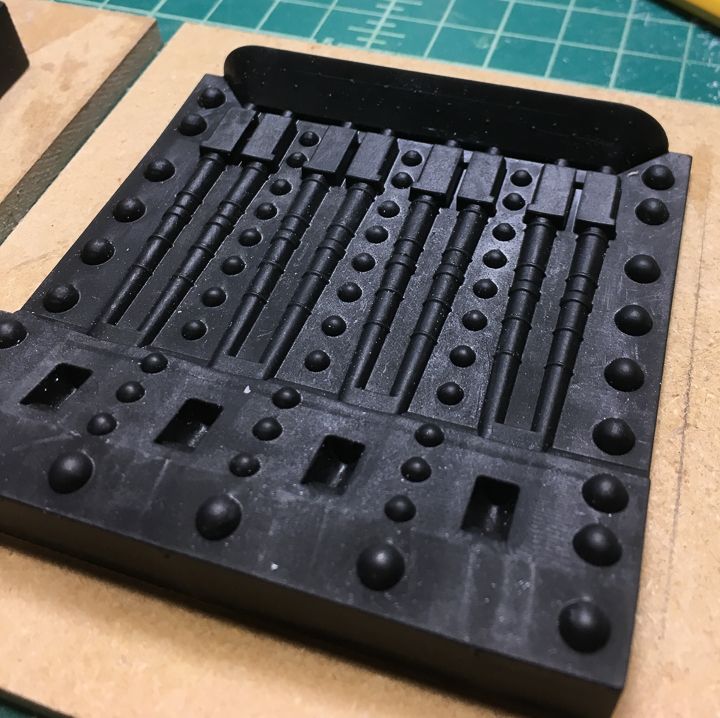
Mold boxes were built around each of the printed parts and the two silicone mold halves poured, much like any other mold.
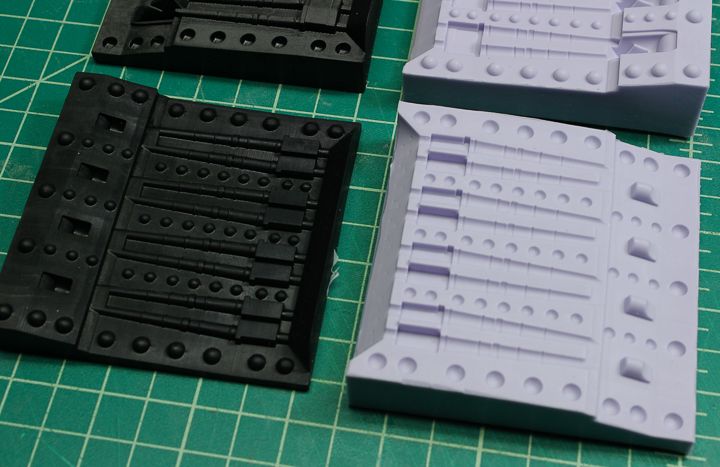
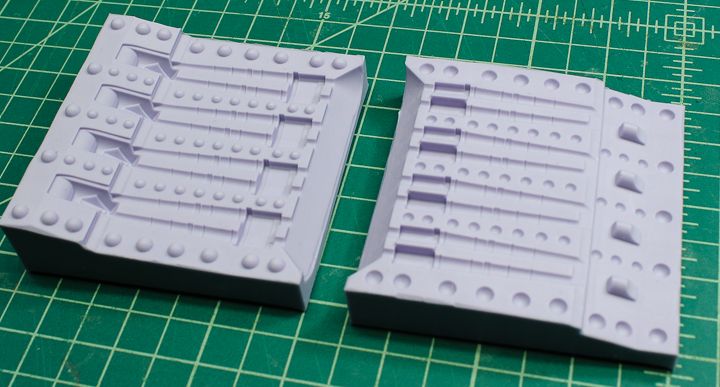
The two mold halves keyed and fit together perfectly!
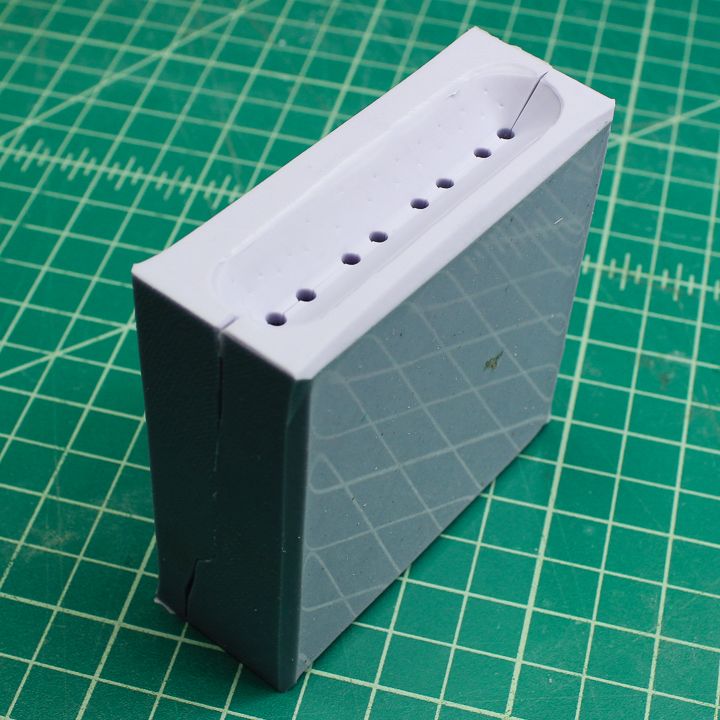
And they worked perfectly and effortlessly. The quality of the surface of the original 3d printed masters is just exceptional. Not only is this a much easier and cleaner way to make a two part mold (but not cheaper, prints from these machines are expensive) but if the mold wears out (typically after 20 to 30 pours) making a new set of molds is straight forward.
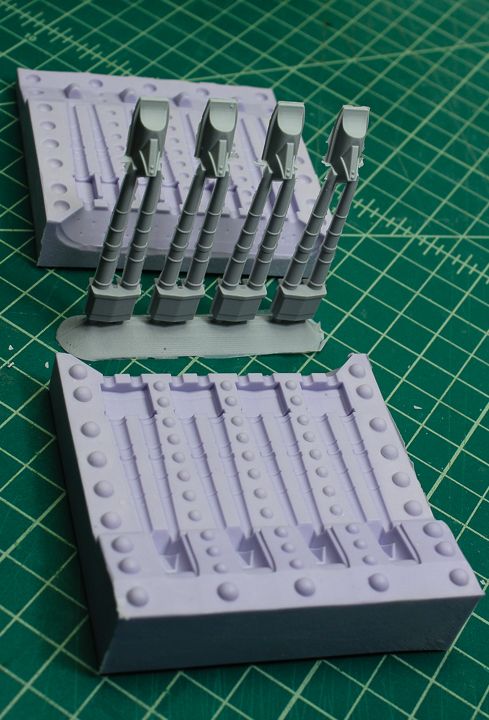
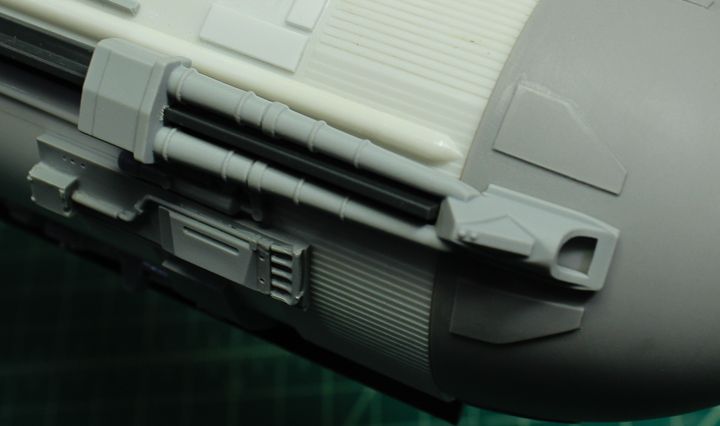
I love tech!
Instead, since the part was 3D modeled, I basically made two separate 3D models of a set of four of the parts, side by side, as they would be embedded in a mold surface, complete with keys and a fill port. There were two models, one for each side. These were then 3D printed at high resolution.
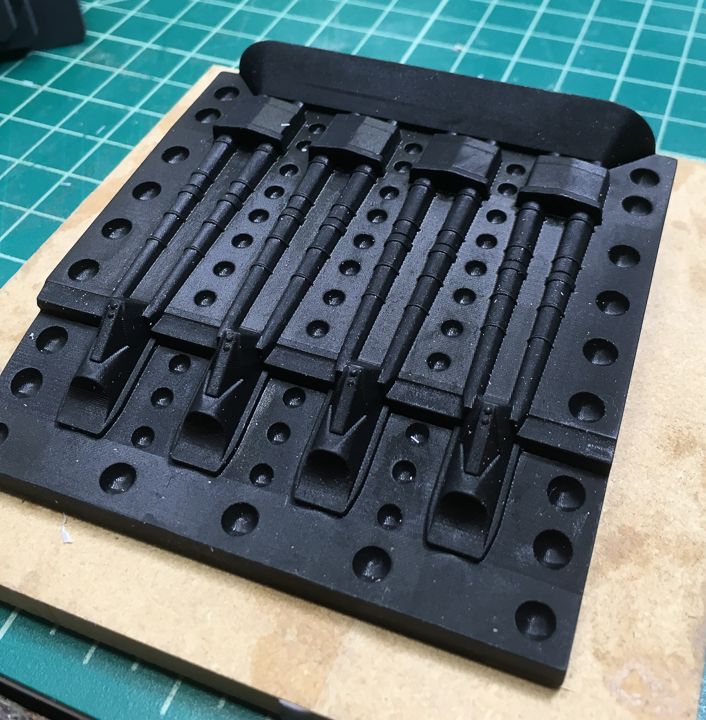
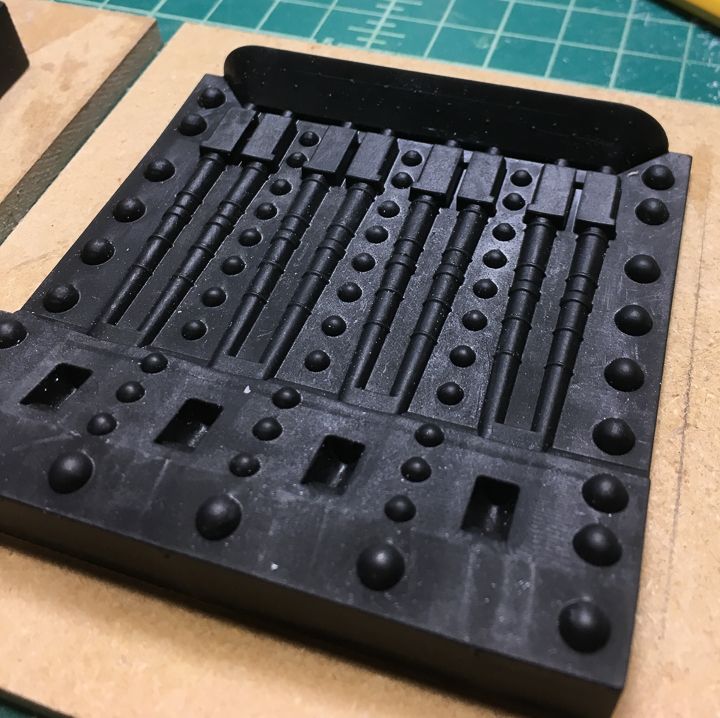
Mold boxes were built around each of the printed parts and the two silicone mold halves poured, much like any other mold.
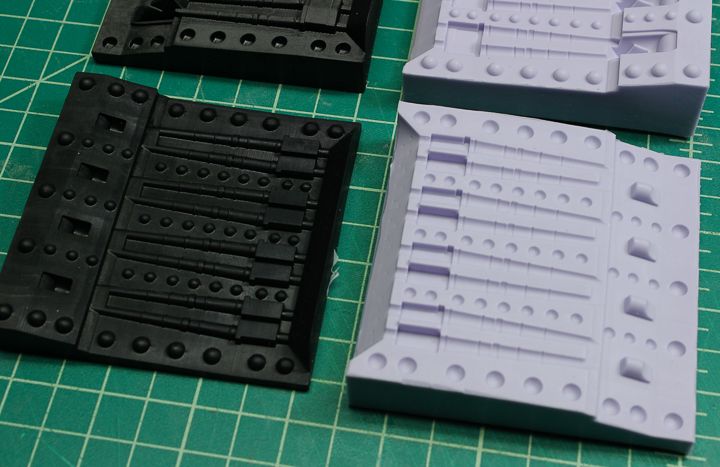
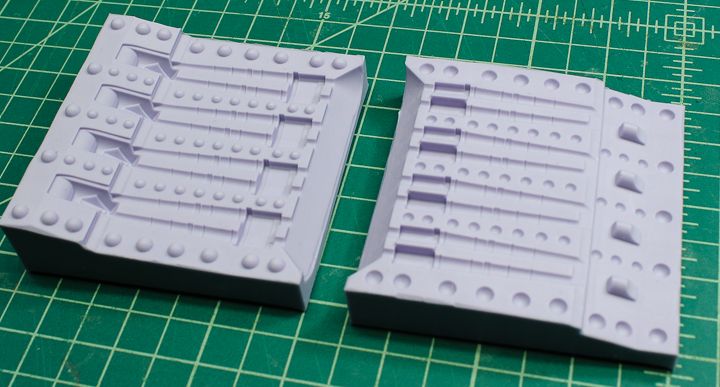
The two mold halves keyed and fit together perfectly!
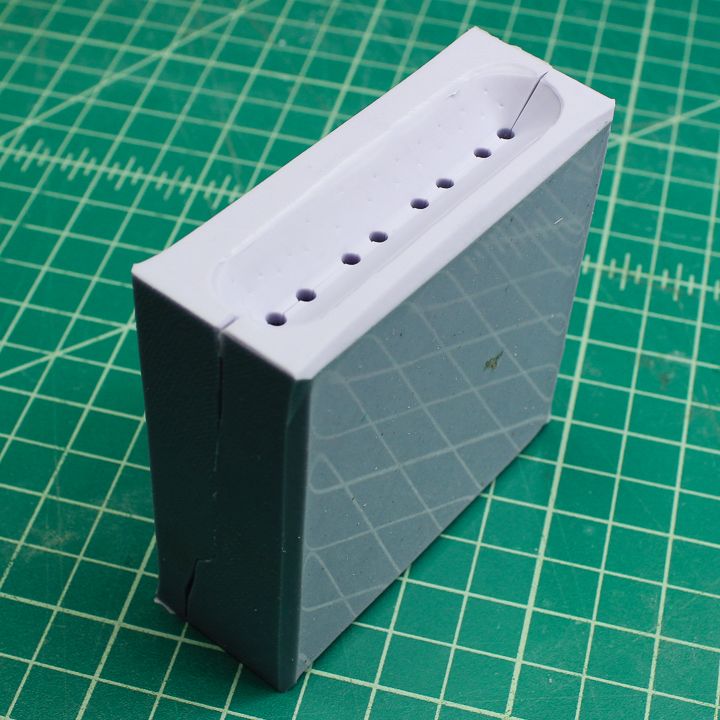
And they worked perfectly and effortlessly. The quality of the surface of the original 3d printed masters is just exceptional. Not only is this a much easier and cleaner way to make a two part mold (but not cheaper, prints from these machines are expensive) but if the mold wears out (typically after 20 to 30 pours) making a new set of molds is straight forward.
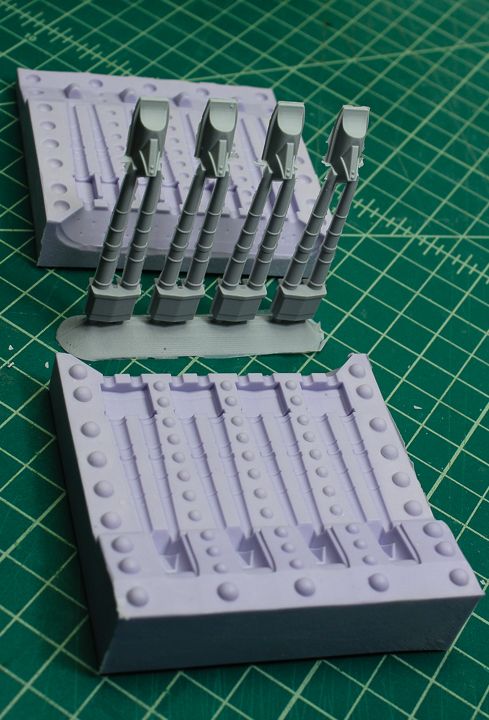
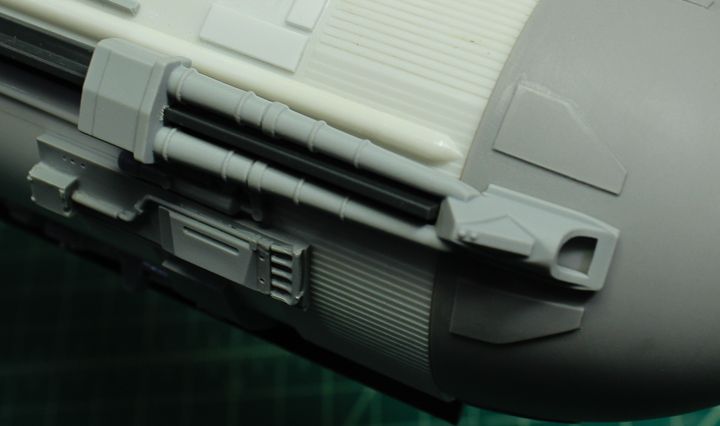
I love tech!